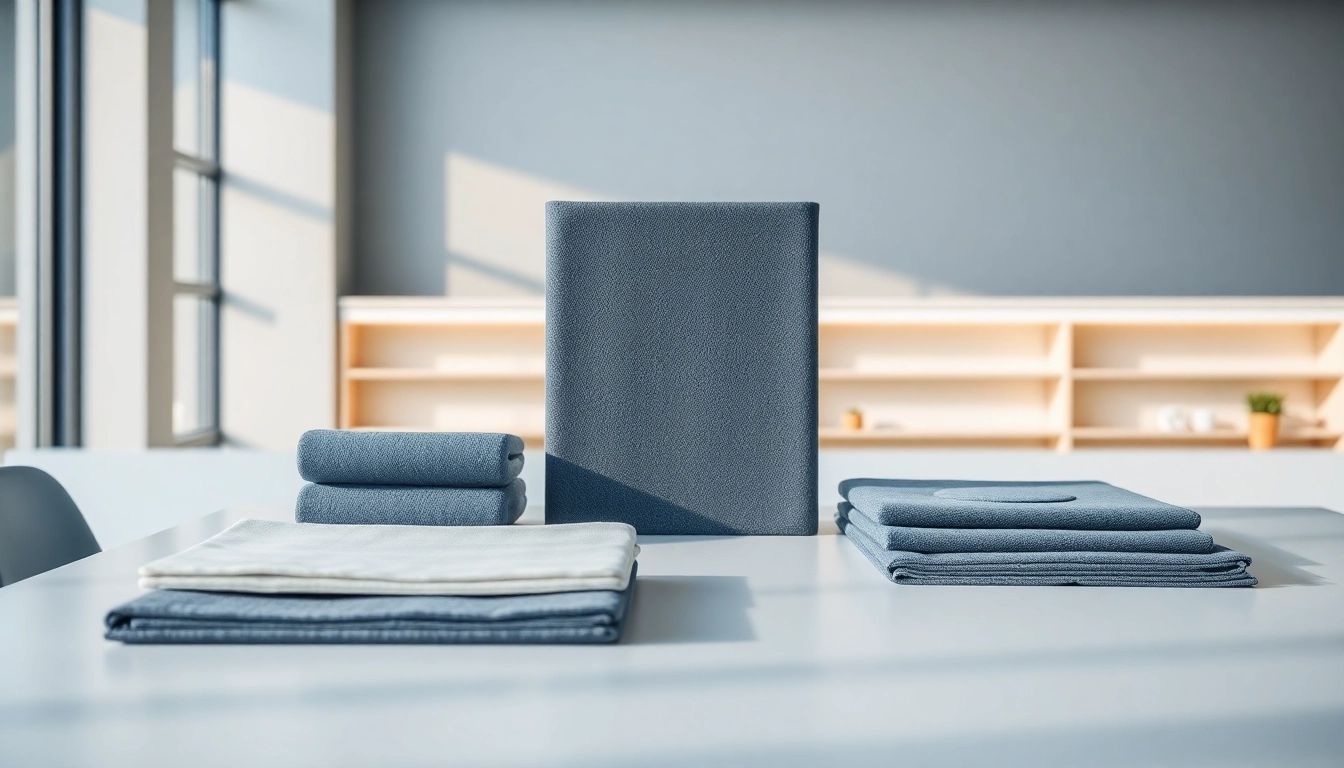
Introduction to Thermal Management Materials
In today’s technology-driven landscape, the effective management of heat is critically important. As electronic devices become smaller and more powerful, the challenges associated with heat dissipation are ever-growing. This is where thermal management materials come into play. These materials provide essential solutions for controlling heat in various applications, thereby improving the performance and longevity of electronic components.
Definition and Importance
Thermal management materials refer to a broad category of products designed to facilitate the efficient transfer, dissipation, or insulation of heat in electronic applications. These materials can significantly reduce thermal resistance, thus ensuring that devices operate within acceptable temperature ranges. The importance of these materials cannot be overstated; as devices generate heat during operation, effective thermal management prevents overheating, which can lead to failure or reduced performance.
Applications in Electronics
Thermal management materials are utilized in a variety of electronic devices, including consumer electronics, automotive applications, and industrial machinery. In consumer electronics, such as smartphones and laptops, these materials help to manage heat generated by processors, batteries, and other components. In the automotive industry, thermal management solutions are employed to manage heat in electric vehicle batteries and power electronics, ensuring safety and efficiency. Industrial machinery also relies on these materials for maintaining optimal operating conditions in heavy equipment, where excessive heat can lead to malfunctions.
Key Properties to Consider
When selecting thermal management materials, several key properties need to be considered:
- Thermal Conductivity: A measure of a material’s ability to conduct heat, which is crucial for effective heat dissipation.
- Mechanical Compliance: The ability of a material to conform to surfaces, which can improve thermal contact and overall performance.
- Temperature Stability: The ability of a material to maintain its properties over a wide temperature range.
- Dielectric Properties: Important for insulating materials that will be used in electronic circuits.
- Ease of Application: The complexity involved in applying the material can impact manufacturing efficiency.
Types of Thermal Management Materials
Thermal Interface Materials (TIM)
Thermal Interface Materials (TIM) are critical in enhancing the thermal connection between various components, such as heat sinks and processors. TIMs can help to fill in microscopic air gaps between uneven surfaces, which improves heat transfer efficiency. Common types of TIMs include thermal pastes, pads, and adhesive films.
For example, thermal pastes are often used in CPU cooling, while thermal pads provide a more simplified application and can be easily cut to fit different sizes. These materials must be carefully selected based on their thermal conductivity ratings, which typically range from 1 to 15 W/mK for traditional compounds, while advanced formulations can exceed 30 W/mK.
Gap Fillers and Thermal Pads
Gap fillers offer a more effective solution for larger air gaps, ensuring a consistent thermal interface even in unevenly spaced applications. They are commonly used where traditional TIMs cannot adequately bridge the gap between a heat-generating device and a heat sink.
Thermal pads are soft, conformable materials that provide a thermal interface in electronic assemblies. They can easily be applied without the need for complicated installation equipment, making them a popular choice in many manufacturing environments. Their ability to dampen vibrations while maintaining good thermal conductivity is an added benefit in delicate electronic devices.
Phase Change Materials (PCM)
Phase Change Materials (PCMs) are innovative thermal management solutions that absorb, store, and release heat as they transition between solid and liquid states. This thermal regulation capability makes them ideal for applications with varying thermal loads, such as power electronics and other heat-sensitive components.
PCMs are particularly valuable in applications where space is at a premium, as they can help to maintain thermal stability without the need for bulky heatsinks or fans. Their effectiveness is often evaluated based on the melting point, specific heat capacity, and thermal conductivity, making them integral in modern electronic designs.
How to Choose the Right Thermal Management Material
Assessing Thermal Conductivity
The first step in selecting the appropriate thermal management material is to evaluate its thermal conductivity. Materials with higher thermal conductivity are generally preferred, as they facilitate better heat transfer. Comparing the conductivity ratings of various materials allows engineers to select ones that align with the specific thermal performance needs of their applications.
For example, materials such as aluminum oxide and copper oxide rank highly due to their excellent thermal transfer properties, making them suitable for high-performance applications.
Evaluating Mechanical Properties
In addition to thermal conductivity, mechanical properties such as compressibility, tensile strength, and modulus of elasticity must be taken into account. These properties help determine how well a material will perform under load and its ability to conform to the surfaces it connects. In applications where flexibility is necessary, such as between complex shapes, softer materials may be employed despite their lower thermal conductivity.
Considerations for Application Environments
Every application environment presents unique challenges, including exposure to moisture, temperature extremes, and vibration. As such, the selected thermal management material should be compatible with its operating conditions. For example, in an automotive environment, materials must withstand exposure to chemicals, while aerospace applications may require lightweight solutions that maintain performance at extreme altitudes.
Conducting a thorough assessment of the environmental factors ensures that the materials chosen can reliably perform over the intended lifecycle of the product.
Best Practices for Implementation
Installation Techniques
Proper installation of thermal management materials is crucial for achieving optimal performance. This entails ensuring that surfaces are clean and free of contaminants before application, as any debris can interfere with effective heat transfer. Applying the right amount of material is also vital; too little may create gaps, while an excess can impede heat transfer.
For TIMs, techniques such as spreading, stamping, or die-cutting can enhance contact quality. Manufacturers often provide guidelines on application methods to ensure the best possible performance from their materials.
Maintenance of Thermal Management Solutions
Regular maintenance can significantly extend the lifespan and performance of thermal management systems. This involves routine inspections of thermal pads, especially in high-stress environments where material degradation may occur. Replacing degraded materials promptly can prevent critical failures in electronic systems.
In applications where maintenance is feasible, reapplication of thermal interface materials, especially after service intervals or during routine checks, can be beneficial.
Performance Monitoring and Adjustment
Monitoring the performance of thermal management systems is key to ensuring optimal operation. This may involve thermographic inspections, temperature sensors, and regular thermal mapping to identify hotspots or areas where performance is degraded.
Adjustments may include re-calibrating cooling fans, applying additional thermal material, or modifying the system design to enhance airflow and heat transfer. Utilizing performance metrics helps to verify that the selected materials are achieving the desired thermal performance levels.
Future Trends in Thermal Management
Advancements in Material Science
Researchers are continuously exploring new materials and formulations that offer improved thermal management capabilities. Graphene, for instance, has emerged as a promising option due to its extraordinary thermal conductivity, mechanical strength, and lightweight properties. Innovations in nanotechnology are also paving the way for materials that can provide exceptional performance in smaller, more compact forms.
As material science progresses, the integration of hybrid materials that combine multiple properties is likely to enhance operational efficiency further, opening new avenues for thermal management.
Integration with Electronic Design
The evolution of electronic design will increasingly incorporate thermal management features from the ground up. This means considering heat dissipation strategies earlier in the design process to avoid costly retrofitting later.
Engineering design tools that simulate heat flow and material interactions are becoming integral to the design phase, allowing for optimized layouts that enhance thermal management capabilities while maintaining space and performance targets.
Sustainability Focus in Material Development
As industries strive for sustainability, the development of eco-friendly thermal management materials becomes paramount. Biodegradable options, recyclable materials, and responsibly sourced compounds are trends that align with the global push towards environmental stewardship.
Companies are beginning to prioritize materials that not only perform well but also reduce environmental impact, making sustainable thermal management solutions a competitive edge in the market.