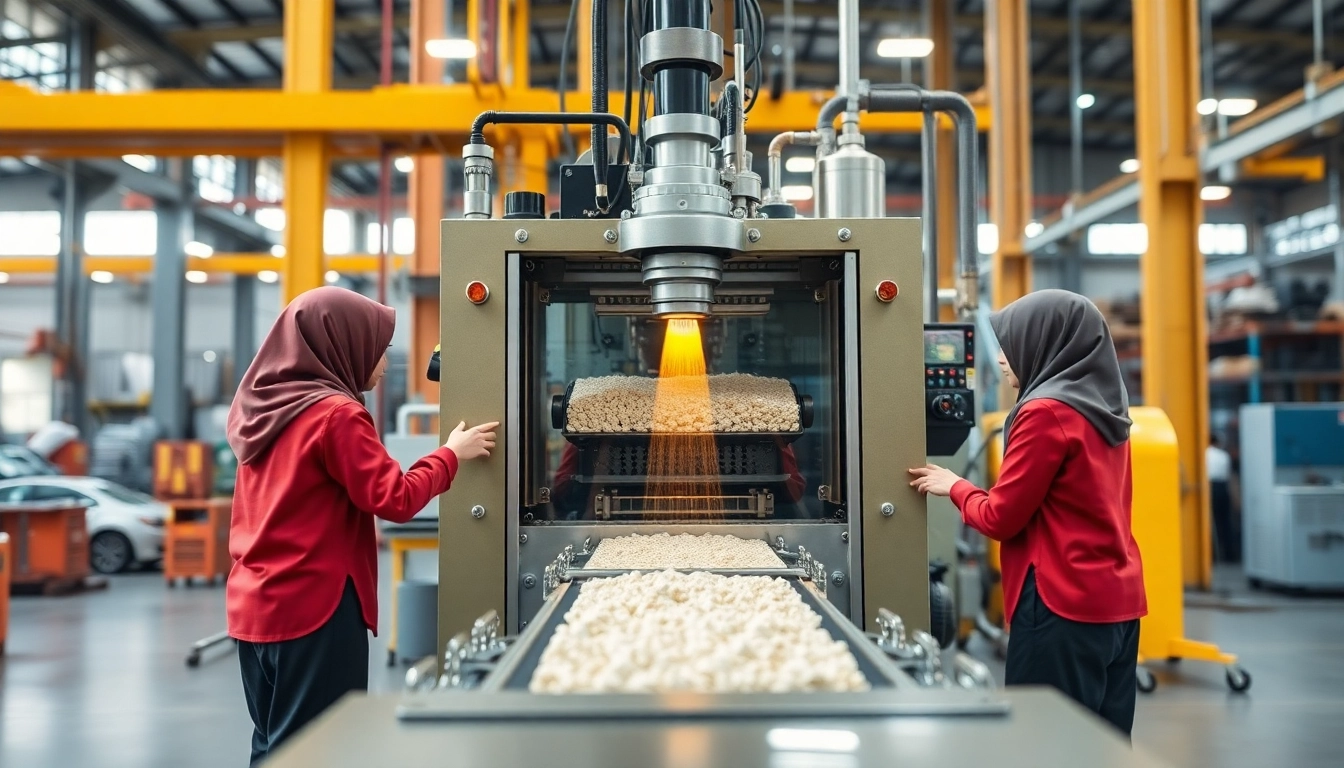
Introduction to Filling Machines
In the world of manufacturing, efficiency and precision are paramount. Filling machines play a crucial role in industries ranging from food and beverage to pharmaceuticals and cosmetics. These machines are designed to accurately dispense liquids, powders, and other materials into various containers, ensuring consistent product quality and optimal production speeds.
This article explores the significance, functionality, types, selection criteria, best practices, and real-world applications of filling machines. Understanding these facets can empower businesses to enhance their operational workflows and maintain competitive advantage in their respective markets.
What is a Filling Machine?
A filling machine is a specialized piece of equipment used to dispense a predetermined amount of product into containers such as bottles, jars, or cans. These machines can fill various types of substances, including liquids, powders, and granules, adapting to the needs of various industries.
The Importance of Filling Machines in the Production Process
Filling machines are integral to production lines, significantly impacting productivity and efficiency. Key reasons for their importance include:
- Consistency: Filling machines ensure each container is filled to the precise amount required, reducing discrepancies and ensuring product reliability.
- Speed: Automated filling machines operate at high speeds, drastically reducing the time needed for manual filling processes.
- Waste Reduction: By accurately measuring and dispensing the correct amounts of product, filling machines minimize waste and save costs.
- Compliance: Many industries are governed by strict regulations regarding product content and packaging, making accurate filling essential for compliance.
How Filling Machines Work
Filling machines operate using various methods depending on the type of machine and product being filled. Below are the main operational principles:
- Volumetric Filling: Measures specific volumes of liquid and dispenses that exact amount into containers.
- Weight Filling: Utilizes scales to fill containers by weight, ensuring each one meets required specifications.
- Time-Based Filling: Distributes liquids based on a predetermined time interval; effective for fluids with a consistent flow rate.
The choice of operation method depends on the nature of the product and the filling machine’s design.
Types of Filling Machines
Manual vs. Semi-Automatic Filling
Filling machines can be classified based on their level of automation:
- Manual Filling Machines: These require full operator involvement and are suitable for small-scale operations or businesses just starting. They are cost-effective but time-consuming.
- Semi-Automatic Filling Machines: These machines require minimal operator intervention. They enhance speed and accuracy while still being affordable for medium-sized operations.
Automatic Filling Machines: Advantages and Challenges
Automatic filling machines offer numerous benefits:
- Labor Savings: Reduced labor costs as these machines require fewer operators and provide a streamlined production process.
- Increased Throughput: Capable of filling products at an unparalleled speed, boosting overall production capacity.
- Enhanced Accuracy: Minimized human error ensures precision filling.
However, challenges may include:
- High Initial Investment: The upfront costs can be significant for automatic filling machines.
- Maintenance Needs: Regular maintenance is essential to ensure optimal performance.
Volumetric Filling Machines: Why Choose Them?
Volumetric filling machines are popular across various industries due to their accuracy and ease of use. They are particularly effective for filling liquids and pastes. Key benefits include:
- Precision: They accurately measure and fill the exact volume required, minimizing product loss.
- Versatility: Suitable for a variety of container sizes and product consistencies.
- Efficiency: Reduced filling time leads to increased overall production efficiency.
Factors Affecting the Selection of Filling Machines
Size and Type of Product
Understanding the type and consistency of the product to be filled is critical in selecting an appropriate filling machine. For instance:
- Thin liquids like water may utilize different filling technologies than thick pastes like peanut butter.
- Specific containers might require specialized machines to fit the nozzle or dispensing method.
Budget and Operational Costs
Investing in a filling machine necessitates a careful budget assessment. Factors to consider:
- Initial Purchase Cost: Evaluate the upfront cost compared to projected efficiency gains.
- Maintenance Costs: Ongoing expenditures for repairs and upkeep should be factored in.
- Cost per Fill: Derive metrics to understand the long-term value based on the machine’s output and efficiency.
Quality and Production Speed Requirements
Another crucial aspect involves understanding customer expectations regarding product quality and delivery timelines. Consider these points:
- Output Speed: Determine the required speed for production to keep pace with market demands.
- Quality Control: Ensure the machine has features that support quality checks throughout the filling process.
Best Practices for Using Filling Machines
Maintenance and Machine Care
Regular maintenance is necessary to extend the lifespan of filling machines. Recommended practices include:
- Scheduled Cleaning: Regularly clean components to prevent contamination and mechanical failures.
- Routine Inspections: Check for wear and tear, particularly on elements subject to frequent use.
Operator Training for Maximum Efficiency
Proper training ensures that operators use the machines effectively. Strategies include:
- Comprehensive Training: Provide detailed operational training covering machine functionalities and troubleshooting.
- Regular Refresher Courses: Keep staff updated with new technologies and practices.
Optimizing Filling Processes for Better Performance
Process optimization involves analyzing workflows to enhance efficiency. Steps to consider include:
- Data Analysis: Monitor and analyze data to identify bottlenecks in the filling process.
- Upgrading Technology: Invest in new technologies or updates to current machines for increased capability.
Case Studies and Applications
Success Stories in Filling Machine Implementations
Examining successful implementations can offer invaluable insights. Below are two notable examples:
- Beverage Industry: A well-known company transitioned to an automatic filling system, which increased productivity by 40% and significantly reduced waste.
- Pharmaceutical Sector: By investing in volumetric filling machines, a local manufacturer enhanced compliance with stringent regulations and improved product safety.
Cost-benefit Analysis of Investing in Filling Machines
Conducting a cost-benefit analysis is essential before making an investment. Consider these aspects:
- Long-Term Savings: While initial costs may be high, evaluate potential savings in labor and material waste.
- ROI Measurement: Monitor performance metrics post-implementation to gauge improvements in throughput and quality.
Challenges Faced and Solutions Implemented
While transitioning to automated filling operations can present challenges, strategic solutions can mitigate these issues:
- Technical Difficulties: Invest in thorough training and maintenance protocols to manage issues quickly.
- Change Resistance: Engage employees in the process by communicating the benefits of automation and involving them in training sessions.
Conclusion
Filling machines have revolutionized the landscape of production in various industries. From enhancing efficiency to ensuring compliance and maintaining product quality, these machines are pivotal in modern manufacturing. By understanding their operational capacities, selecting the appropriate technology, and adhering to best practices, businesses can position themselves for success and sustainability in an increasingly competitive marketplace.