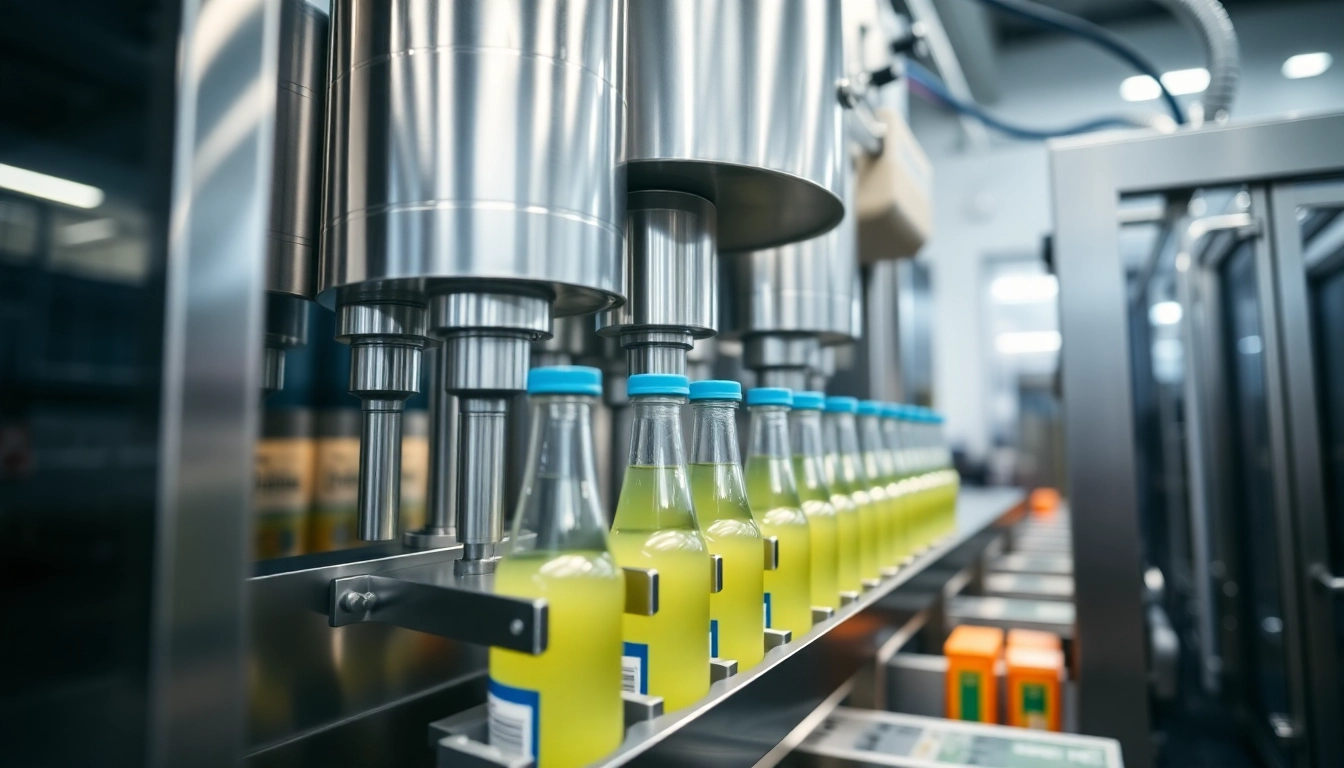
Understanding Filling Machines
The Filling Machine has become an essential piece of equipment in various sectors such as food and beverage, pharmaceuticals, and cosmetics. These machines are designed to automate the process of filling containers with liquids, powders, and other materials, thereby improving efficiency and consistency in production. In this section, we will dive into what a filling machine is, explore the different types available, and discuss their applications across various industries.
What is a Filling Machine?
A filling machine is an industrial machine that dispenses a specific volume of product into a container, which can include bottles, boxes, or pouches. The primary goal of filling machines is to enhance production capabilities while minimizing manual labor and reducing human error. By employing various technologies, these machines can fill products with high precision, ensuring that each container is filled to the required level accurately.
Filling machines can be categorized based on their working principles and automation levels, which leads us to explore the next section on types of filling machines.
Types of Filling Machines
The diversity of filling machines available today can be overwhelming. They can be classified based on the type of product they handle, their automation capabilities, and the filling principles they employ. Below, we discuss the primary classifications:
1. By Automation Level
Filling machines can be broadly categorized into three primary levels of automation:
- Manual Filling Machines: These are operated by hand and require the operator to fill each container manually. While they are less expensive, they are labor-intensive and often slow compared to automated alternatives.
- Semi-Automatic Filling Machines: These devices require some level of human involvement but automate key processes such as filling and capping. They are suitable for businesses that require flexibility without fully committing to automation.
- Fully Automatic Filling Machines: These machines operate independently, handling the entire process from filling to capping and labeling with minimal human intervention. They are ideal for high-volume production lines.
2. By Filling Mechanism
Filling machines can also be categorized based on the filling mechanisms they utilize:
- Piston Fillers: These machines use a piston to draw liquid into a chamber and then push it into the container. They are widely used for products that have varying viscosities, including creams and sauces.
- Gravity Fillers: This type relies on gravity to fill containers, making it suitable for free-flowing liquids like water or juices. It is less precise than piston mechanisms but often used for high-speed filling operations.
- Vacuum Fillers: These machines use vacuum pressure to fill containers. They are particularly beneficial for beverages and sensitive products, as they minimize the risk of spills and bubbles.
- Auger Fillers: Often used for powders and granules, auger fillers rely on a rotating auger to transport and dispense the product into containers.
Applications in Different Industries
Filling machines find applications in a range of industries due to their versatility and adaptability. Here are some key sectors that benefit from filling technology:
1. Food and Beverage
In the food and beverage industry, filling machines are essential for packaging liquids like wine, juices, sauces, and oils. They ensure hygiene standards while maximizing production speed, which is crucial for meeting consumer demand. Automated solutions can quickly fill bottles with various volumes, maintaining consistent quality and reducing waste.
2. Pharmaceuticals
The pharmaceutical industry relies heavily on precision and contamination control, making filling machines vital for packaging medicines, syrups, and lotions. Machines in this sector follow stringent regulatory standards, ensuring that products are filled accurately and safely, which is critical for both patient safety and legal compliance.
3. Cosmetics
The cosmetics industry uses filling machines for products like creams, lotions, and fragrances. Given the high value and often delicate nature of cosmetics, these machines must ensure accuracy and prevent contamination, which can damage products and affect brand reputation.
4. Chemical Industry
In chemical manufacturing, filling machines are necessary for safely handling corrosive and hazardous materials. Companies must choose machines designed specifically for the properties of the fluids being processed, ensuring safety for workers and compliance with regulations.
Key Features of Modern Filling Machines
As technology evolves, modern filling machines come equipped with advanced features that enhance their operational efficiency and usability. Here are some of the crucial features to look for:
Automation Capabilities
Today’s filling machines integrate automation features that streamline the filling process significantly. Advanced models often incorporate sensors, software, and robotics to perform tasks automatically, which reduces labor costs and minimizes human error. Features like auto-stop filling, which detects when a bottle is full and stops the flow of liquid, further enhance productivity. Automation not only speeds up production but also improves traceability and quality control, which are essential in industries with strict regulatory requirements.
Accuracy and Precision
Modern filling machines are built for accuracy. With advancements in technology, machines are designed to deliver precise measurements for various products. Features such as volume control, measuring devices, and software algorithms allow for precise fill rates, which are crucial for industries like pharmaceuticals and food and beverage, where accuracy can affect product quality and consumer safety.
Ease of Use and Maintenance
User-friendly controls, intuitive interfaces, and easy setup procedures are increasingly important in filling machines to accommodate a diverse range of operators. Additionally, the ease of maintenance is critical for minimizing downtime. Machines designed with easy access to critical components can significantly reduce the time and effort required for routine maintenance and troubleshooting, helping ensure more consistent operational uptime.
Choosing the Right Filling Machine
When looking to invest in a filling machine, it is essential to carefully assess various factors to ensure that the chosen machine fits operational needs. Below are key considerations when making this decision:
Assessing Your Production Needs
The first step in selecting a filling machine is to analyze your production volume and the types of products you need to fill. If your operations require high throughput, a fully automatic machine might be necessary. Conversely, if your production needs are more modest, a semi-automatic machine may suffice. Understanding your filling speed requirements, container types, and product characteristics will guide the selection process effectively.
Budget Considerations
Budget is a critical component of any investment decision. Determine the financial investment you can make in a filling machine without compromising quality and operational demands. It is essential to evaluate not just the initial acquisition cost but also the total cost of ownership, including maintenance, repairs, and potential upgrades. Investing in a higher-quality machine initially may save costs in the long run by reducing downtime and maintenance expenses.
Vendor Reliability and Support
Choosing a reputable vendor with a track record of reliability and strong customer support is paramount. Look for manufacturers with positive reviews, warranties, and robust after-sales support. A vendor that offers training, assistance with operational issues, and readily available spare parts can greatly enhance machine performance and reliability, ensuring continuity in production.
Best Practices for Operating Filling Machines
To maximize the efficiency and longevity of filling machines, operators should follow best practices. Proper operational protocols lead to improved productivity, safety, and product quality. Below are essential guidelines to consider:
Regular Maintenance Tips
Routine maintenance is vital to keep filling machines functioning optimally. This includes:
- Conducting regular cleaning to prevent the buildup of residues.
- Checking mechanical parts for wear and tear, replacing components as necessary.
- Inspecting electrical systems and software for updates to ensure they are running efficiently.
- Implementing a maintenance log to track repairs, replacements, and routine service schedules.
Operator Training Essentials
Comprehensive training for operators on the correct use of filling machines is crucial. Training should cover:
- Operating procedures, including starting, stopping, and troubleshooting common issues.
- Understanding machine functions and safety features to minimize the risk of accidents.
- Regular procedures for cleaning and maintaining the machine to ensure optimal performance.
Safety Protocols
Establishing safety protocols is crucial to minimize accidents and injuries when operating filling machines. Key safety measures include:
- Ensuring all operators wear appropriate personal protective equipment (PPE).
- Conducting routine safety checks to identify potential hazards.
- Training staff on emergency procedures and first-aid measures in case of accidents.
Future Trends in Filling Technology
As technology continues to evolve, several trends are shaping the future of filling machines. Staying abreast of these advancements can benefit companies looking to maintain a competitive edge:
Integration with IoT
The integration of Internet of Things (IoT) technology into filling machines allows for enhanced monitoring and control. IoT-enabled machines can provide real-time data regarding production metrics, machine health, and maintenance needs. This capability enables predictive maintenance, allowing companies to proactively address issues before they lead to machine failures, thereby minimizing downtime and loss of productivity.
Energy Efficiency Improvements
With increasing emphasis on sustainability, filling machines are evolving to become more energy-efficient. Manufacturers are adopting eco-friendly technologies that minimize energy consumption without sacrificing performance. These innovations help companies reduce their carbon footprints and operational costs, contributing positively to their sustainability goals.
Innovations in Filling Materials
The materials used in filling operations are also undergoing transformation. Advanced materials that are lightweight yet durable are being utilized for containers, enhancing both logistics and sustainability. Attention is also being given to recyclable and biodegradable materials that cater to eco-conscious consumers, and this trend is likely to grow.