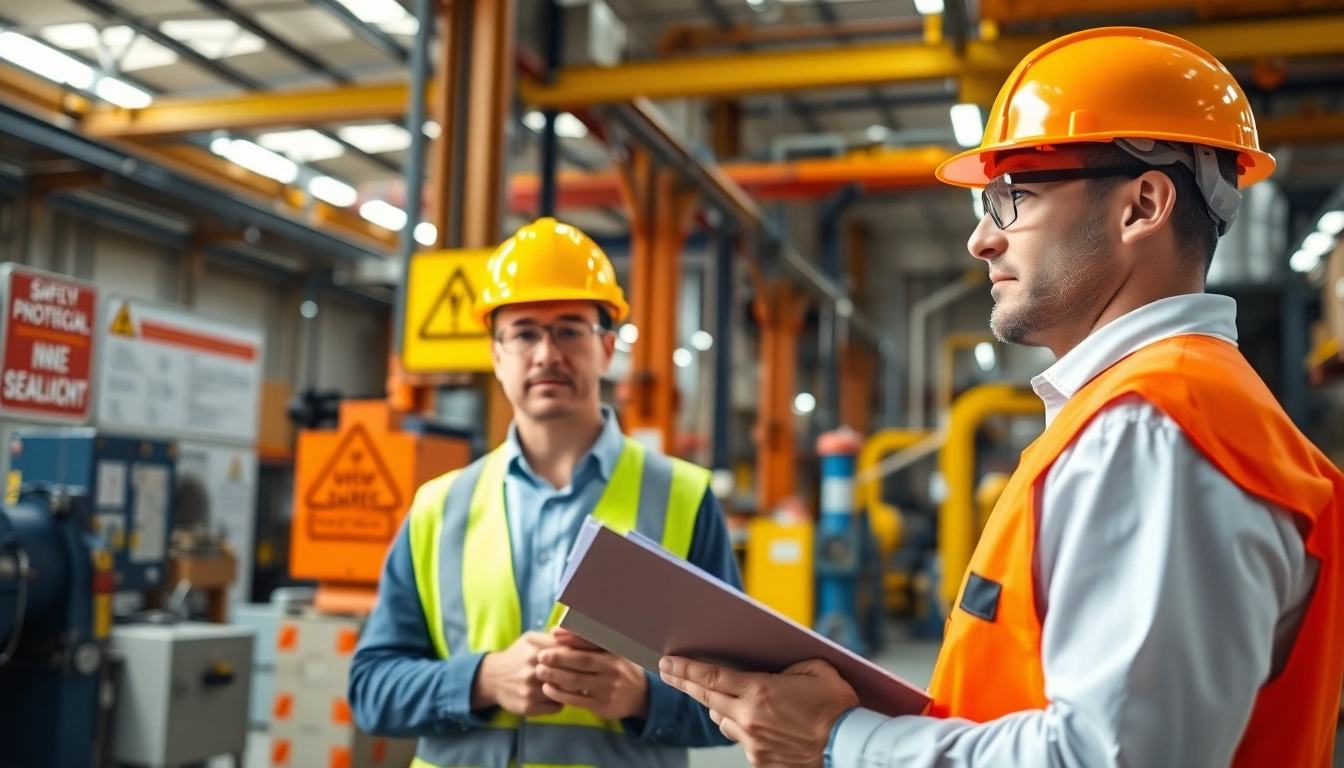
Understanding the Role of a St. George Industrial Safety Consultant
In today’s rapidly evolving industrial landscape, the importance of safety cannot be overstated. A St. George Industrial Safety Consultant serves as a vital resource for organizations seeking to enhance their workplace safety protocols and ensure compliance with stringent regulations. This article delves into the multifaceted role of safety consultants, their necessary skills, and their significance in maintaining safe industrial environments.
What Does an Industrial Safety Consultant Do?
An industrial safety consultant provides expert guidance to organizations on how to manage and mitigate safety risks within the workplace. Their primary responsibilities include conducting risk assessments, developing safety programs, and training employees in best safety practices. These consultants act as liaisons between regulatory agencies and businesses to ensure that safety standards are not only met but exceeded. Furthermore, they help organizations prepare for audits and inspections, which are critical for maintaining operational licenses and satisfying legal obligations.
Key Skills and Qualifications Required
To be effective in their role, industrial safety consultants should possess a variety of skills and qualifications. Key among them are:
- Education: A degree in occupational safety, environmental science, or a related field is often essential.
- Certifications: Credentials such as Certified Safety Professional (CSP) or Occupational Health and Safety Technologist (OHST) enhance credibility.
- Experience: Practical experience in various industrial settings is crucial for understanding the specific hazards inherent to different sectors.
- Communication Skills: The ability to convey complex safety concepts in an accessible manner is vital for training and reporting.
- Analytical Skills: Proficiency in analyzing data and interpreting regulations is essential to develop effective safety protocols.
Defining Industrial Safety Standards in St. George
In St. George, industrial safety standards are dictated by both federal regulations and local ordinances. Familiarity with bodies such as the Occupational Safety and Health Administration (OSHA) is critical for consultants who wish to develop compliant safety programs. Furthermore, consultants must stay abreast of evolving laws and technologies to ensure that safety programs incorporate the latest best practices. By integrating local industry specifics with broader safety standards, consultants can tailor their recommendations to meet the unique needs of St. George’s diverse industrial landscape.
Identifying Workplace Safety Hazards
A significant aspect of an industrial safety consultant’s job is identifying potential hazards that could compromise employee safety. This process not only enhances workplace safety but also contributes to improved productivity and morale among employees.
Common Risks in Industrial Environments
Industrial environments present numerous risks that can lead to accidents and injuries. Common hazards include:
- Mechanical Hazards: Involving equipment malfunction or improper use of machinery.
- Chemical Hazards: Exposure to toxic substances, often prevalent in manufacturing and chemical plants.
- Ergonomic Hazards: Resulting from repetitive tasks that lead to musculoskeletal disorders.
- Electrical Hazards: Can arise from improper wiring or the use of defective electrical equipment.
- Slips, Trips, and Falls: Frequently occurring in environments with cluttered pathways or wet floors.
Assessing Risk Levels Effectively
Effective risk assessment involves identifying hazards and evaluating the risk associated with them. This assessment can be conducted through various methodologies such as:
- Qualitative Assessments: Using interviews and surveys to establish perceived risks among employees.
- Quantitative Assessments: Utilizing statistical analysis to measure incidents and near misses.
- Job Safety Analysis (JSA): This breaks down job tasks into steps, examining the risks associated with each step.
By identifying potential hazards and their risk levels accurately, safety consultants can create targeted interventions to mitigate these risks effectively.
Tools and Techniques for Hazard Identification
To identify hazards effectively, safety consultants employ various tools and techniques. These include:
- Checklists: Structured lists to ensure all potential hazards are examined during inspections.
- Safety Audits: Comprehensive reviews of existing safety protocols and workplace conditions.
- Incident Reporting Systems: Tools that allow employees to report hazards or unsafe practices anonymously.
- Observation Techniques: Directly observing work practices to identify unsafe behaviors or conditions.
Combining these tools enhances the depth of hazard identification processes, ensuring that consultants can address all potential safety issues adequately.
Implementing Effective Safety Protocols
After identifying workplace hazards, the next critical step for safety consultants is to implement effective safety protocols designed to mitigate those risks.
Creating a Comprehensive Safety Plan
A comprehensive safety plan serves as a roadmap for implementing safety procedures within an organization. Essential components of an effective safety plan include:
- Safety Policies: Defined rules and guidelines for maintaining workplace safety.
- Emergency Response Plans: Procedures to follow in the event of accidents or emergencies.
- Maintenance Programs: Regular inspection and maintenance of equipment to prevent malfunctions.
- Reporting Procedures: Clear steps on how employees should report hazards or incidents.
By documenting these components, organizations can ensure that all employees understand their roles in maintaining a safe workplace.
Employee Training and Involvement Strategies
Training is critical to the success of any safety protocol. Effective training programs should be interactive, engaging, and relevant to the employees’ roles. Strategies include:
- Hands-on Workshops: Providing practical experience in safe operation methods and emergency response situations.
- Regular Refresher Courses: Ensuring ongoing education about new safety protocols and updates.
- Incentivizing Safety: Implementing reward systems for teams that adhere to safety guidelines diligently.
Involving employees in the creation and implementation of these programs fosters a safety culture where everyone takes responsibility for workplace safety.
Measuring Compliance with Safety Standards
To ensure the effectiveness of implemented safety protocols, measuring compliance is essential. This can be achieved through:
- Regular Inspections: Scheduled audits to evaluate adherence to safety standards.
- Incident Tracking: Keeping detailed records of safety incidents to identify trends over time.
- Feedback Mechanisms: Soliciting employee feedback on the safety program’s effectiveness and areas for improvement.
By consistently measuring compliance, organizations can adapt their safety programs to respond to any emerging risks or changes in regulations.
Case Studies: Successful Safety Consulting in St. George
Real-world examples can illustrate the profound impact of effective safety consulting. Here, we highlight a few success stories from local industries in St. George.
Success Stories from Local Industries
One notable example comes from a manufacturing company in St. George that faced significant safety challenges due to outdated equipment and unclear safety protocols. After engaging an industrial safety consultant, they conducted a thorough risk assessment followed by immediate action:
- Upgrading machinery to meet safety standards.
- Implementing a comprehensive training program for all employees.
- Regular safety audits to ensure ongoing compliance and to adapt the training as needed.
As a result, the company reported a 50% reduction in workplace incidents over just one year, showcasing the potential benefits of effective safety consulting.
Lessons Learned from Implemented Safety Programs
The key takeaway from these success stories highlights the importance of employee involvement and continuous improvement in safety protocols. Effective communication regarding safety measures and providing employees a platform to express concerns can significantly improve overall safety performance in any organization.
Transforming Safety Culture in Organizations
Consultants not only enhance safety measures but also contribute to cultural shifts within organizations. A manufacturing plant in St. George that integrated safety as a core value into its operations saw a marked transformation:
- Employee morale improved significantly as individuals felt valued and cared for.
- Increased productivity was observed as safety protocols minimized downtime.
- A culture of open communication was fostered, where employees felt empowered to report hazards without fear of reprisal.
This holistic approach demonstrated that safety is not merely a compliance issue, but an integral component of workplace success.
The Future of Industrial Safety Consulting
The field of industrial safety consulting is constantly evolving, influenced by various emerging trends and technologies.
Trends Affecting the Industry
Safety consultants must be aware of key trends shaping the industry, including:
- Increased Regulation: Expect heightened scrutiny from regulatory agencies as governments prioritize worker safety further.
- Focus on Mental Health: The growing acknowledgment of mental well-being highlights the need for comprehensive safety policies that consider psychological risks.
- Holistic Well-being: Organizations are now looking at overall employee well-being, integrating safety into broader health and wellness initiatives.
Staying informed of these trends allows safety consultants to provide the most relevant advice to their clients.
Technology’s Role in Enhancing Safety Measures
Advancements in technology are revolutionizing safety practices. Innovative tools such as:
- Wearable Devices: Monitoring employee health metrics can provide real-time data on potential safety risks.
- Virtual Reality (VR): Immersive training experiences enhance employee preparedness for real-life scenarios.
- Mobile Applications: Facilitate quick reporting of incidents or hazards while also offering instant access to safety protocols.
These technologies not only streamline safety processes but also provide a more engaging approach to safety training.
Opportunities for Growth in Safety Consulting
As industry needs evolve, the demand for skilled safety consultants will likely increase. Opportunities to explore include:
- Specialization: Consultants with specialized knowledge in certain industries will be increasingly sought after.
- Advisory Roles: As organizations strive for continuous improvement, consultants can take on advisory positions within companies.
- Training Development: Creating and offering industry-specific training programs can position consultants as thought leaders in their field.
By adapting to these new opportunities, safety consultants can ensure their practices remain relevant and impactful in a changing industrial landscape.