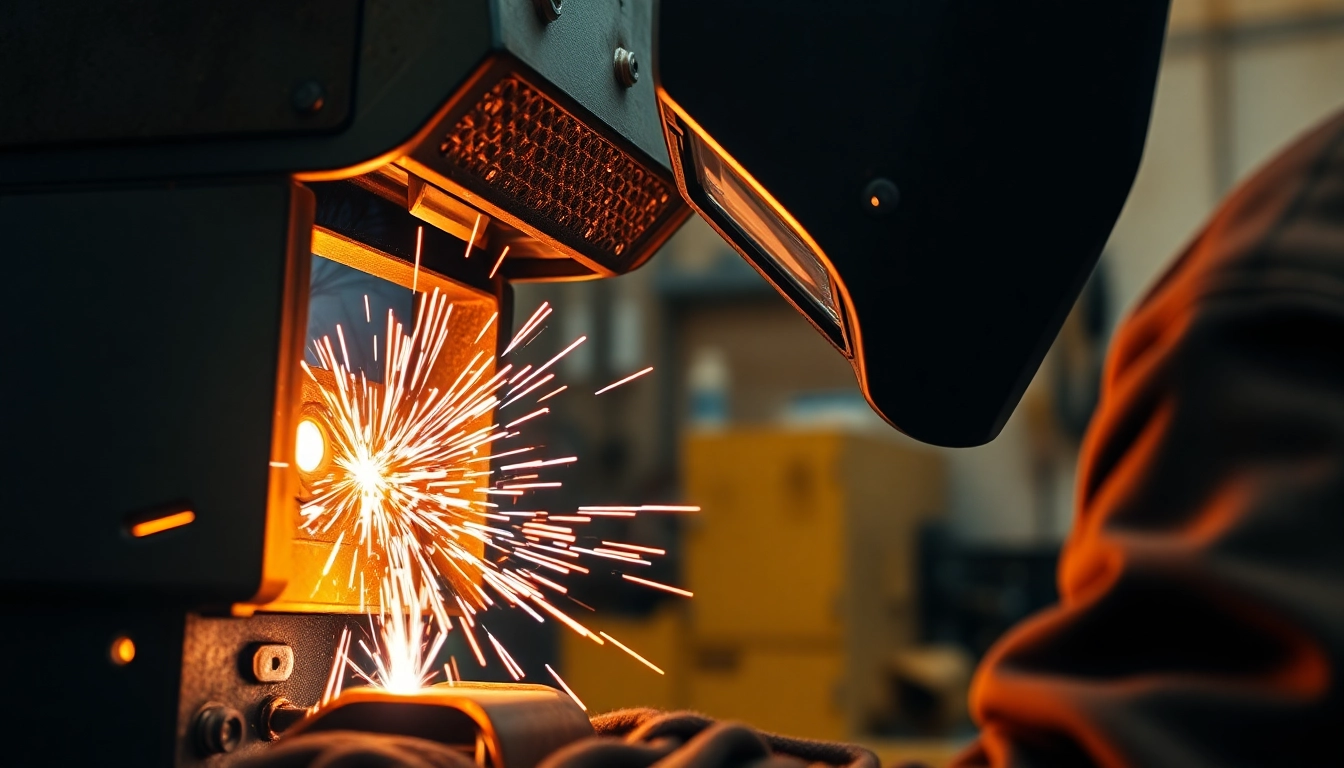
Understanding AC DC TIG Welding
What is an AC DC TIG Welder?
An AC DC TIG welder is an advanced welding machine that can operate using both alternating current (AC) and direct current (DC). This versatility is particularly beneficial for welding a wide range of metals, including aluminum, stainless steel, carbon steel, copper, titanium, and nickel alloys. By being able to switch between AC and DC, welders can adjust their techniques and settings according to the requirements of the specific project at hand. Essentially, the ac dc tig welder becomes a multi-purpose tool suitable for various applications within the welding industry.
How AC vs. DC Affects Welding Quality
The choice between AC and DC can significantly affect the quality and characteristics of the weld. Alternating current (AC) is primarily used for welding aluminum because it provides a cleaning action during the welding process. This cleaning cycle helps to remove the oxides present on the surface of aluminum, allowing for better penetration and weld quality. On the other hand, direct current (DC) is more commonly used for welding ferrous metals, as it allows for deeper penetration and produces a cleaner weld with fewer welding defects. The flexibility to select between these two options enables welders to produce high-quality, durable joints tailored to specific material types and welding conditions.
Common Applications of AC DC TIG Welding
AC DC TIG welding is employed across various industries due to its versatility and precision. Some common applications include:
- Automotive Industry: Used for chassis and body seals where aluminum welding is often required.
- Aerospace: Suitable for components requiring lightweight and high-strength materials, often utilizing aluminum and titanium alloys.
- Fabrication Shops: Perfect for custom metalworks where different materials are used, providing welders the flexibility needed for diverse projects.
- Marine Applications: Often used in shipbuilding and repair where aluminum is prevalent due to its corrosion resistance.
Selecting the Right AC DC TIG Welder
Key Features to Consider
When selecting an AC DC TIG welder, several key features should be taken into account:
- Output Power: The welder’s amperage range dictates the thickness of the material that can be welded. Look for a welder with sufficient power to handle your projects.
- Pulse Settings: Pulse welding capabilities are essential for controlling heat input and minimizing distortion on thin materials.
- Portability: Evaluate whether a portable unit is necessary depending on the nature of your work and workspaces.
- Welding Torch Type: The type of torch influences ease of use; options include air-cooled and water-cooled torches with different specifications.
- Duty Cycle: The duty cycle indicates how long the machine can operate before needing a cool-down period. A higher duty cycle is preferable for continuous work.
Top Brands in the Market
The market for AC DC TIG welders is competitive, featuring several reputable brands known for quality and reliability. Some top brands include:
- Miller Electric: Recognized for innovation and durability, Miller offers a range of TIG welders suitable for both hobbyists and professionals.
- Thermal Dynamics: Their machines are known for high performance and efficiency, catering to industrial applications.
- Everlast: Known for affordability, Everlast offers a wide range of TIG welders that incorporate modern features.
- Lincoln Electric: A leader in welding equipment, Lincoln Electric products are revered for robustness and precision.
Budget Considerations for Your Purchase
Establishing a budget is crucial before purchasing any welding machinery, including AC DC TIG welders. Prices can vary significantly based on features, brand, and capabilities. Basic models might cost around $500, while high-end industrial models can exceed $5,000. It is vital to balance features and budget, ensuring that you select a welder that meets your needs without overspending. Consider additional costs such as accessories, consumables, and maintenance when planning your budget.
Setting Up Your AC DC TIG Welder
Essential Tools and Accessories
A well-equipped workspace is critical for effective TIG welding. Key tools and accessories include:
- TIG Welding Torch: A proper torch that suits your welder is essential for achieving good results.
- Tungsten Electrodes: The choice of tungsten depends on the material you are welding; this affects the quality of the arc.
- Filler Rods: Select appropriate filler rods that match the base materials for appropriate bonding.
- Gas Bottle and Regulator: Ensure that the shielding gas is correct for your welding needs, with argon being a common choice.
- Personal Protective Equipment (PPE): Safety gear, including gloves, welding helmets, and appropriate clothing, is crucial to protect against sparks and UV exposure.
Safety Precautions to Follow
Safety should always be a priority when operating an AC DC TIG welder. Follow these precautions:
- Wear proper PPE to prevent injuries from UV radiation and hot material.
- Avoid welding in damp or unventilated areas to prevent electric shock.
- Ensure your workspace is clear of flammable materials.
- Familiarize yourself with the welder’s manual and operational procedures.
Adjusting Settings for Optimal Performance
Properly adjusting the settings on your AC DC TIG welder is vital for achieving the best results.
Start by setting the correct amperage based on the thickness of the metal and the type of material you are using.
For aluminum, use AC settings, and for most ferrous metals, opt for DC.
Additionally, familiarize yourself with various pulse options and how they can reduce heat input while improving weld quality on thin materials.
Regularly check technique and progression speed to maintain a consistent bead and avoid defects such as undercutting or burn-through.
Techniques for Effective TIG Welding
Mastering the Weld Pool Control
Controlling the weld pool is essential for achieving high-quality welds. Effective weld pool control is about managing heat input and movement.
Start by maintaining a steady hand and adjusting your travel speed based on the alloy and thickness.
A good practice is to move in a consistent pattern, allowing the heat to evenly distribute across the weld area.
Experiment with techniques like “weaving” to improve fusion on wider joints, but ensure that the puddle remains consistently molten.
Tips for Welding Different Metals
Different metals require specific approaches in TIG welding:
- Aluminum: Use AC settings and ensure that the surface is clean to prevent contamination. The cleaning action of AC helps remove oxides.
- Stainless Steel: Use DC and a lower amperage to prevent overheating and warping. Ensure good gas coverage to avoid oxidation.
- Copper: A higher heat input is necessary; preheating can help manage the thermal conductivity of copper.
- Titanium: Work in an inert atmosphere to avoid oxidation, making use of DC modes to minimize heat input.
Common Mistakes and How to Avoid Them
New welders often encounter several common mistakes. Here are ways to avoid them:
- Inconsistent Beads: Achieve a steady travel speed and avoid jerky motions to maintain smooth and consistent bead appearance.
- Burn-Through: Excessive heat can cause burn-through on thin metals; manage your amperage and travel speed effectively.
- Poor Gas Coverage: Ensure proper flow rates and gas coverage to reduce oxidation and rework on joints.
Maintenance and Troubleshooting of TIG Welders
Routine Maintenance Tips
Regular maintenance is crucial for ensuring optimal performance and extending the life of your AC DC TIG welder. Key maintenance tips include:
- Regularly check and replace tungsten electrodes to ensure optimal arc stability.
- Inspect hoses and connections for leaks or wear regularly.
- Clean the torch regularly to prevent buildup that could impact performance.
- Keep the cooling system (if applicable) in check for proper coolant levels and functioning.
Troubleshooting Common Issues
Even with proper maintenance, issues may arise. Here are some common problems and how to troubleshoot them:
- Inconsistent Arc: Check for gas flow issues, electrode condition, and proper settings.
- Overheating: Ensure the duty cycle is observed and the cooling system is operational.
- Poor Penetration: Adjust the amperage and focus on your technique, ensuring a steady travel speed.
Extending the Life of Your AC DC TIG Welder
Extending the lifespan of your AC DC TIG welder is achievable through proper care and use. Regularly maintain it, keep it clean, and store it in a stable environment.
Training and experience play a significant role in reducing wear and tear. Invest time in learning how to properly set up, operate, and maintain your machine.
Moreover, adhering to manufacturer’s guidelines for routine maintenance will ensure the welder remains in good working condition for years to come.