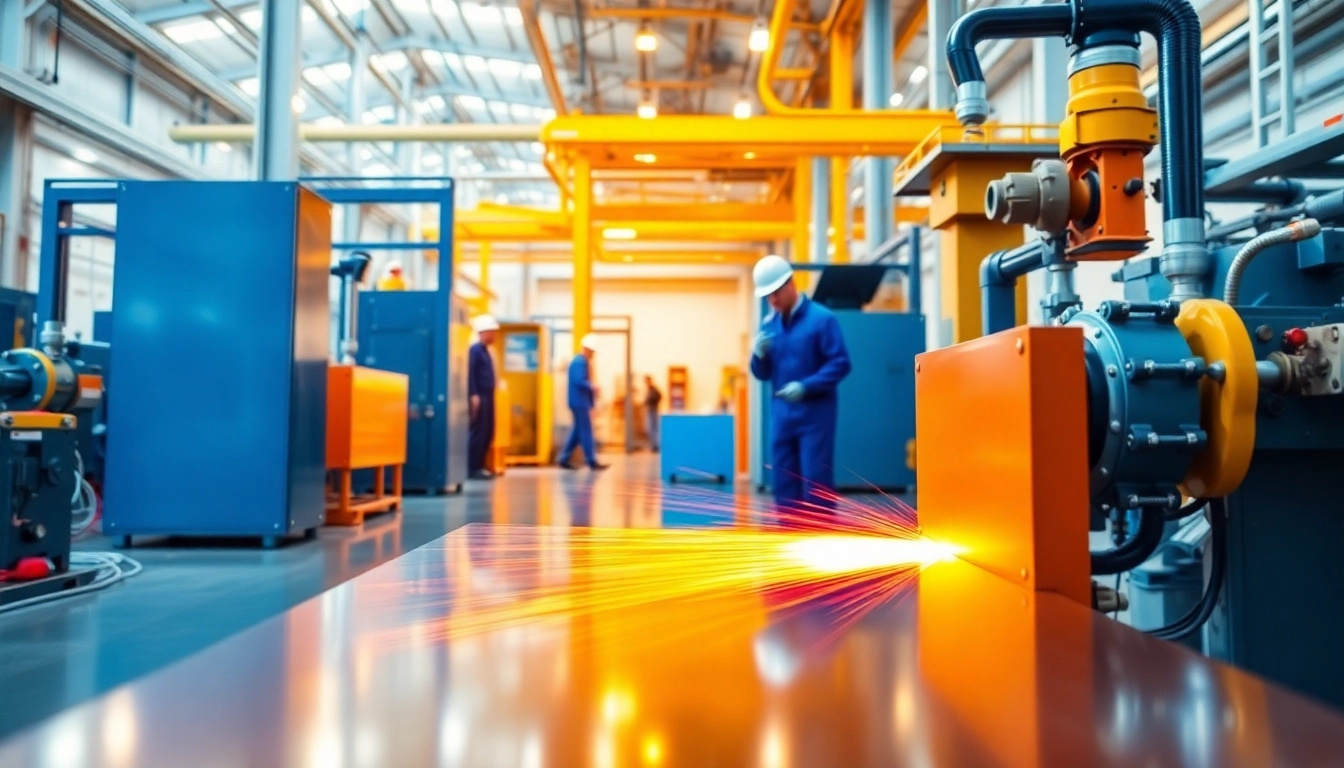
Understanding Ecoating: What Is It?
Ecoating, also known as electrophoretic painting or E-coat, is a surface finishing process that uses electrical currents to apply paint to conductive materials. This technique is renowned for its uniform coating distribution and exceptional corrosion resistance, making it a preferred choice across various industries. In the ecoating west midlands, manufacturers have embraced this technology for its efficiency and effectiveness in enhancing product durability.
The Basics of Ecoating Technology
The core concept behind ecoating is simple yet effective. It involves submerging the workpieces into a bath containing a water-based paint solution mixed with charged particles. When an electrical current is applied, these particles migrate to the positively or negatively charged surfaces of the workpiece, adhering firmly. This method not only allows for a thicker, more even coat but also ensures that hard-to-reach areas are adequately covered.
Benefits of Using Ecoating
Ecoating provides several advantages that make it a superior choice for surface coating:
- Enhanced Corrosion Resistance: The electrocoating process creates a robust protective layer that significantly enhances the longevity of the product, especially in harsh environments.
- Uniform Coverage: The process effectively covers complex shapes and designs, ensuring that every nook and cranny receives adequate protection.
- Environmental Friendliness: Ecoating is a water-based process that minimizes volatile organic compounds (VOCs), making it a more environmentally friendly option compared to traditional solvent-based paints.
- Cost-Effectiveness: With reduced wastage and better application efficiency, ecoating proves to be economically beneficial in the long run.
How Ecoating Differs from Traditional Coating Methods
Traditional coating methods, such as spray painting or powder coating, often struggle with even coverage and consistency, especially on intricate components. In contrast, ecoating’s electrochemical process ensures that paint is deposited evenly, eliminating drips or runs in the finish. Furthermore, ecoating achieves better adhesion and long-term bond strength due to the chemical reaction during the process, something that traditional methods may lack.
Applications of Ecoating in Different Industries
Ecoating finds applications in numerous industries due to its versatility and effectiveness. Here are some prominent sectors benefiting from this innovative technology:
Aerospace Applications for Ecoated Components
The aerospace industry demands precision and durability, making ecoating an ideal choice for coating aircraft components. The lightweight yet resilient finish offered by E-coat aids in improving fuel efficiency by minimizing weight while protecting parts from the harsh conditions encountered at high altitudes. Moreover, ecoated components can withstand the intense vibrations and temperature fluctuations typical in aerospace applications.
Automotive Industry and Ecoating Innovations
In the automotive sector, ecoating serves a critical role in achieving high-quality finishes that are both visually appealing and durable. Manufacturers use E-coat techniques extensively for chassis and body components to enhance rust and corrosion resistance. Innovations such as the application of multi-layer ecoating systems offer further protection, paving the way for extended vehicle lifespans and decreased maintenance costs.
Construction and Equipment Use of Ecoating
Construction equipment and machinery are often exposed to severe conditions, necessitating robust protective coatings. Ecoating provides a strong barrier against rust and wear, which is crucial in construction applications. Additionally, ecoated finishes can withstand harsh chemicals commonly found on construction sites, ensuring equipment longevity and reliability.
Choosing the Right Ecoating Provider in the West Midlands
When seeking ecoating services, particularly in the West Midlands, understanding how to select the right provider is paramount. The following criteria can help guide the decision-making process:
Criteria for Selecting a Quality Ecoating Service
To find a reputable ecoating provider, consider these key factors:
- Certification and Compliance: Check for industry-specific certifications and environmental compliance to ensure quality and safety standards.
- Experience and Expertise: Look for providers with a proven track record in ecoating operations, particularly in your industry.
- Technology and Equipment: Evaluate the technology used in the ecoating process, ensuring they utilize state-of-the-art methods for optimal results.
- Customer Reviews and Testimonials: Research feedback from previous clients to gauge service quality and reliability.
Common Challenges in the Ecoating Process
Despite its advantages, the ecoating process can present several challenges, including:
- Surface Preparation: Proper surface cleaning and preparation are crucial for adhesion; any residue can lead to poor coating quality.
- Environmental Factors: Temperature and humidity levels can impact the electrocoating process. Providers must regulate these factors to maintain quality.
- Curing Process: The curing stage is critical for achieving the desired finish and durability. Monitoring the curing parameters ensures optimal performance.
Evaluating Ecoating Service Providers
When assessing potential ecoating service providers in the West Midlands, focus on their ability to address common challenges effectively. Ask prospective providers detailed questions about their processes, technology, and quality control measures to ensure they can deliver the high standard required for your products.
Best Practices for Ecoating Maintenance and Care
Once ecoated components are in use, proper maintenance is vital to maximizing their lifespan and performance. Here are best practices to consider:
Routine Checks for Ecoated Surfaces
Regular inspections of ecoated surfaces can prevent minor issues from escalating. Look for signs of wear, discoloration, or corrosion, as these can indicate potential problems. Maintaining a routine schedule ensures prompt addressing of any anomalies.
Common Maintenance Tasks for Ecoated Items
Maintenance tasks for ecoated items may include:
- Cleaning: Use mild detergents and non-abrasive cloths to clean ecoated surfaces, avoiding harsh chemicals that could damage the finish.
- Touch-ups: Small scratches or chips can be repaired with additional ecoating material to maintain integrity and appearance.
- Monitoring Environmental Conditions: Keep a watch for environmental factors—excessive moisture and humidity can impact the performance of the coating.
Long-term Care Tips for Ecoated Products
To ensure the longevity of ecoated products, consider the following tips:
- Storage Conditions: Store ecoated items in controlled environments to limit exposure to extremes in temperature and humidity.
- Proper Handling: Train staff in the correct handling of ecoated products to prevent damage during installation or transportation.
- Regular Maintenance Protocols: Implement comprehensive maintenance protocols that include routine checks and cleaning schedules.
Case Studies: Successful Implementations of Ecoating
Examining real-world applications can provide valuable insights into the effectiveness of ecoating. Here are a few case studies from local businesses:
Innovative Ecoating Solutions in Local Businesses
A local automotive manufacturer recently adopted ecoating technology to enhance their component finishes. By implementing an ecoating line, they significantly reduced their annual maintenance costs and improved product quality. This forward-thinking approach positioned them as leaders in sustainability while meeting stringent industry standards.
Analysis of Ecoating Benefits Achieved
Following the adoption of ecoating, the manufacturer noted a 30% increase in component lifespan and a considerable decrease in warranty claims. The protective benefits of ecoating allowed for greater design flexibility and decreased the need for frequent repairs.
Lessons Learned from Ecoating Projects
Through these implementations, several key lessons emerged:
- Investment in Technology: Investing in modern ecoating technology pays dividends in product quality and operational efficiency.
- Training Personnel: Employee training on new processes ensures smooth transitions and maximizes the benefits of ecoating.
- Feedback Loops: Establishing feedback mechanisms allows for continual improvement and helps address potential issues with the ecoating process.